Magnetic Rotary Position Sensors
Magnetic rotary position sensors (a.k.a. magnetic rotary encoders) are devices which measure the rotation angle of something using magnetism. There are a number of sub-categories of magnetic rotary position sensors including:
- Hall-effect sensors: Use the Hall effect to measure the magnetic field.
- GMR sensors: Use the giant magnetoresistance effect to measure the magnetic field.
Most of these sensors involve attaching a small magnet to the rotor. The rotating magnetic field is then measured contactlessly. The way it is measured it what defines the different sub-classes of sensors.
One of the most simple and common ways of measuring rotation is with a potentiometer which varies resistance as a rotating wiper changes position across a resistive track. However, the benefits of magnetism over a standard resistive potentiometer include:
- Supports continuous rotation with no end stops.
- There is no resistive track/wiper that wears out.
- It’s more resistant to contamination.
- It can be done contactlessly, e.g. with an air-gap or through some materials.
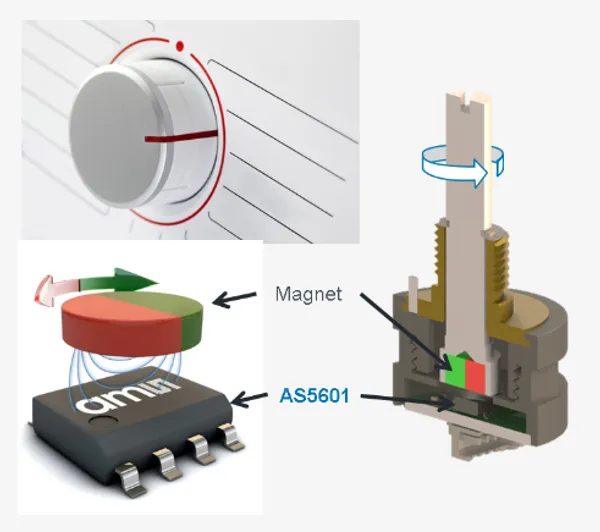
Most of the ICs include a processor to convert the raw magnetic readings into rotational data that can be read back over a communications bus to a microcontroller.
Uses
- Sensing the rotor angle in BLDC and PMSM motors (which you need to know so that you can turn on the correct inverter MOSFETs).
- Sensing the rotation of the steering wheel in vehicles2.
Giant Magnetoresistive (GMR) Sensors
Giant magnetoresistive (GMR) sensors are based on a quantum phenomenon called giant magnetoresistance.
GMR sensors can give a much better SNR than more traditional hall-effect based sensors:
Our GMR design produces more than 50 times the voltage of a Hall element when a magnetic field is applied, which translates to a monumental boost in signal-to-noise ratio (SNR)2.
Gaps of 4-8mm between the magnet and sensing IC can be achieved with standard sized devices.2.
History
Giant magnetoresistance was first discovered in 19883 4. It is an effect that can be measured with nanometer-thick films of magnetic layers separated by similar thickness non-magnetic layers.
It is called “giant” because the multiple layers significantly increases the resistance change due to a magnetic field (can be a 50% change at very low temperatures) over standard “anisotropic” magnetoresistance (which is typically only a few percent)5.
Examples
Infineon TLE5014
Integrated sensor, EEPROM.
There are variants of the TLE5014 for different communication protocols. Supported is the SPC, PWM or the SENT interface for data transfer.
The TLE5014 has variants with fully redundant dual sensors for safety critical applications. To further aide with fault detection, the magnetic sensors are flipped w.r.t. to each other to create inverted outputs, as shown below.
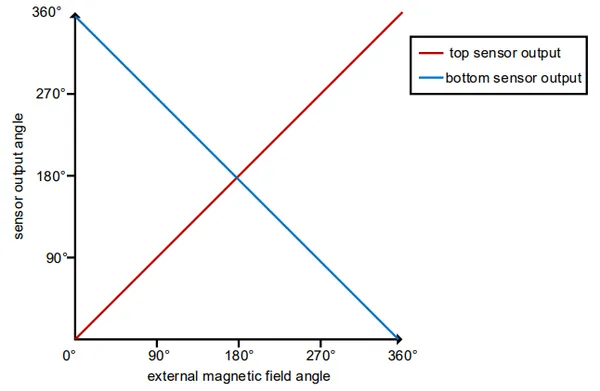
Tunnelling Magnetoresistive (TMR) Sensors
Tunnelling magnetoresistive sensors use a slightly different principle to GMR. A TMR sensor consists of two ferromagnets separated by a nanometer thing insulating barrier. The barrier is thin enough that electrons can tunnel through it (a quantum effect). An external magnetic field can change the magnetization direction of the ferromagnet layers. When the two layers are magnetically aligned there is a higher change of electrons tunnelling through the barrier. When the two layers are in antiparallel there is a lower chance. This changes the effective resistance of the junction, which is then measured to deduce the direction of the magnetic field7.
TMR sensors generally have a better SNR than GMR sensors. The signal of a TMR sensor can be approx. 6 times higher than that of a GMR sensor, and 200 times higher that a hall sensor8.
TMR is used in the read heads of modern hard drives7.
Further Reading
If you are interested in dirt-cheap, basic rotation sensors for things like user interface knobs, you might want to use a potentiometer. Another way of measuring rotation is an optical encoder.
Footnotes
-
AMS-Osram. Reliability to switch on: Small position sensor keeps consumer products running [blog post]. Retrieved 2024-03-28, from https://ams-osram.com/news/blog/magnetic-rotary-position-sensor. ↩
-
Allegro Microsystems (2022, Feb 23). The Future of Automotive Wheel Sensing with GMR. Retrieved 2024-03-29, from https://www.allegromicro.com/en/insights-and-innovations/technical-documents/p0083-future-of-wheel-sensing-gmr. ↩ ↩2 ↩3
-
Wikipedia (2024, Jan 4). Giant magnetoresistance. Retrieved 2024-03-29, from https://en.wikipedia.org/wiki/Giant_magnetoresistance. ↩
-
NVE Corporation. Application Notes for GMR Sensors. Retrieved 2024-03-29, from https://www.nve.com/Downloads/apps.pdf. ↩
-
NVE Corporation. How GMR Works. Retrieved 2024-03-31, from https://www2.nve.com/gmrsensors/gmr-operation.htm. ↩
-
Infineon (2019, May 9). TLE5014SP16D [datasheet]. Retrieved 2024-03-29, from https://www.infineon.com/dgdl/Infineon-TLE5014SP16D%20E0002-DataSheet-v01_00-EN.pdf?fileId=5546d46270c4f93e0170c92e1bc10212. ↩ ↩2
-
Wikipedia (2024, Jan 2). Tunnel magnetoresistance. Retrieved 2024-04-02, from https://en.wikipedia.org/wiki/Tunnel_magnetoresistance. ↩ ↩2
-
TDK. TMR Sensors. Retrieved 2024-04-02, from https://product.tdk.com/en/techlibrary/productoverview/tmr-angle-sensors.html. ↩