PCB Design
Welcome the the PCB Design subsection of the mbedded.ninja blog!
If you are interested in decoupling and noise suppression, check out the Decoupling And Noise Suppression page.
If you are interested in thermal management, see the Heatsinking page.
Child Pages
Decoupling And Noise Suppression
Decoupling And Noise Suppression
Castellation
Castellation
Designators
A tutorial on designator choice and placement during the PCB design process.
Designators
A tutorial on designator choice and placement during the PCB design process.
Desmear And Etchback
Desmear And Etchback
General Routing Tips
General Routing Tips
How To Calculate Maximum Track Current
How To Calculate Maximum Track Current
IMS (Insulated Metal Substrate) PCBs
IMS (Insulated Metal Substrate) PCBs
Mid-Chip Solder Balls
Photos, explanations, solder paste improvements and more info on mid-chip solder balls, a common PCB manufacturing defect.
Mid-Chip Solder Balls
Photos, explanations, solder paste improvements and more info on mid-chip solder balls, a common PCB manufacturing defect.
Layer Stack-up
Layer Stack-up
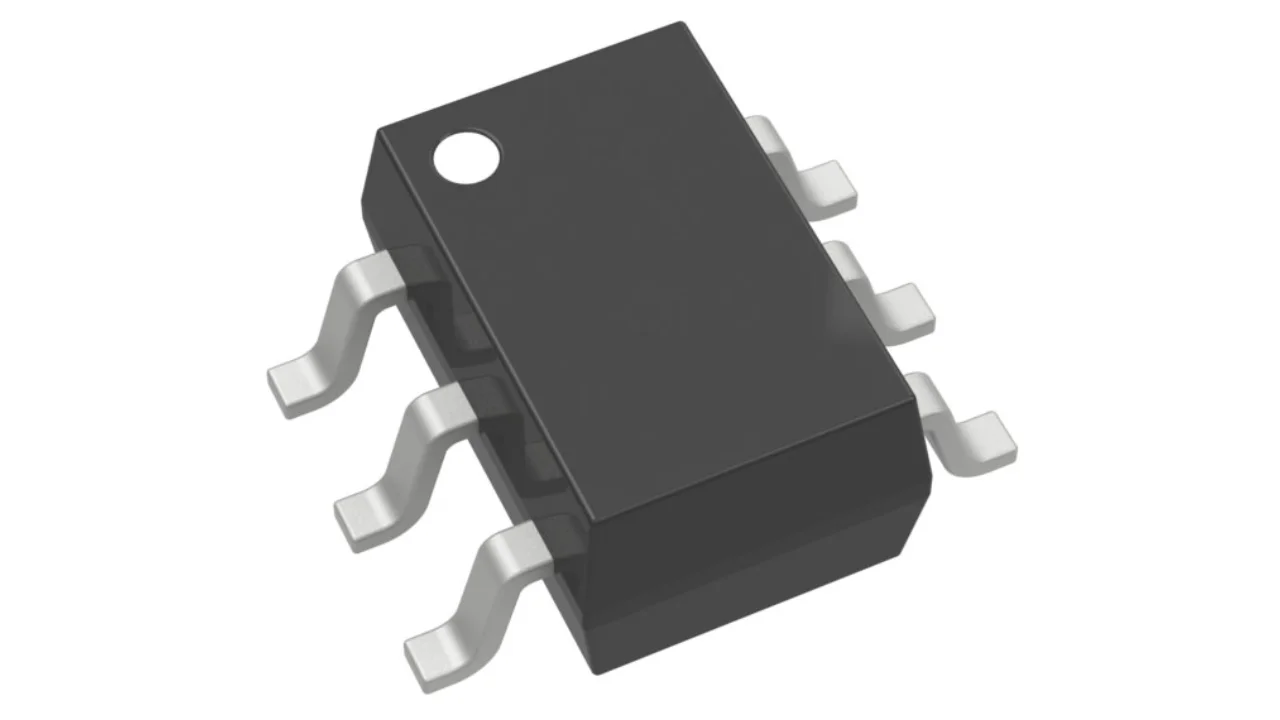
Component packages are the physical body that electronic components are housed in. Many of them are industry standard. This page provides a database of component packages and a reference chart with the dimensions of popular packages.
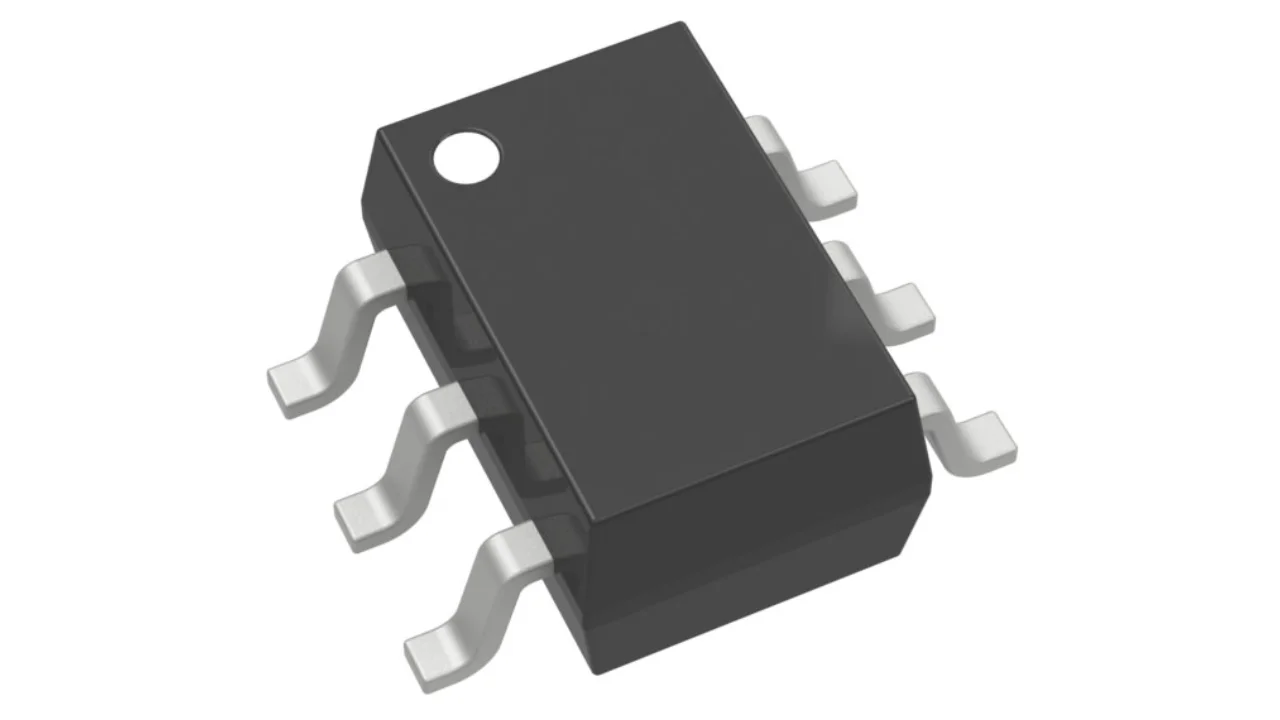
Component Packages
Component packages are the physical body that electronic components are housed in. Many of them are industry standard. This page provides a database of component packages and a reference chart with the dimensions of popular packages.
Mouse Bites
Info on "mouse bites" which are used when panellizing PCBs.
Mouse Bites
Info on "mouse bites" which are used when panellizing PCBs.
Pads, Vias And Holes
All you need to know about pads, vias and holes in a PCB design.
Pads, Vias And Holes
All you need to know about pads, vias and holes in a PCB design.
PCB Data Formats
Gerber files, layers, ODB+, IPC-2581 and more info on PCB data formats.
PCB Data Formats
Gerber files, layers, ODB+, IPC-2581 and more info on PCB data formats.
PCB Design Checklist
PCB Design Checklist
PCB Surface Finishes
PCB Surface Finishes
PCB Design Tools
PCB Design Tools
Soldering
Soldering
Soldermask Stencils
Soldermask Stencils
PCB Layers
PCB Layers
Schematic Tips And Tricks
Schematic Tips And Tricks
Prototyping
Prototyping
Test Jigs
Info on test jigs.
Test Jigs
Info on test jigs.
Testpoints
Testpoints
The PCB Rework Guide
The PCB Rework Guide
Thermal Design For PCBs
Thermal conductivity, the resistance model, TIMs, a via thermal resistance calculator and more info on thermal design for PCBs.
Thermal Design For PCBs
Thermal conductivity, the resistance model, TIMs, a via thermal resistance calculator and more info on thermal design for PCBs.